Within the context of Reliable Manufacturing, precision maintenance is a key element. However, it’s important to remember that “precision alignment” is only one part of precision maintenance — there is a lot more to placing a machine in a precise state than just achieving a value of misalignment at the feet or the coupling. This includes proper identification of machinery errors and the capacity to fix them.
Some examples of common misalignment issues include:
- Thermal growth
- Base problems
- Poor fits
- Short leg
- Soft foot
- Assembly errors
There are many misconceptions about alignment standards. The main arguments focus on whether we should use coupling or foot values to determine whether equipment and overall systems are within tolerance. We’ll first look at some primary trains of thought regarding alignment standards.
Responding to Common Thoughts on Alignment Standards
1. “Use of foot values for alignment standards will not improve machine reliability”
Response: This is quite simple and can be exemplified by asking a simple hypothetical question: “Yes or no, would the bearings and seals of a machine that is aligned to within precision foot tolerances (say 0.002” same-sign) run smoother and last longer than one that is not?”
Most reasonable people would agree that the answer is yes.
We often see articles that state, ” The objective of alignment is to minimize radial forces at the coupling.” Based on our considerable experience in the area, we disagree.
When we study the actual causes of machinery failure in the field, while coupling failures do occur, they are nowhere near as common as failures of bearings and seals. So, a better statement would be: ”The objective of alignment is to extend machine life by minimizing the misalignment conditions at the bearings of the machine, thereby extending the life of the machine.”
2. “Companies must spend an enormous amount of time and labor going the extra mile to achieve high precision alignment standards”
Response: This statement demonstrates a lack of understanding of the precision process and somewhat exaggerates the reality on the ground. Certainly, any organization will have to spend extra time performing pre-alignment checks and pre work. However, this will not be an “enormous” amount of time. In most cases, much of the time expended in the preparation is regained over time when the actual alignment is performed in the form of repeatable readings and accurate moves.
For example, by taking time to clean and inspect the base and effectively identify and eliminate both short leg and angular soft foot, some major sources of frustration and error are “pre-eliminated,” resulting in significant time savings. Another source of inconsistency is not using torque wrenches to tighten holding-down bolts. Most reasonable people agree that tightening a fastener with a torque wrench does not take significantly longer than with a regular wrench.
3. “The foot value method will frustrate and discourage aligners who are motivated to perform precision maintenance as very small measurement errors will result in large foot value fluctuation”
Response: There is a reasonable amount of validity to this statement. Measurement errors do cause frustration and can certainly be discouraging. Therefore, everything that can be done to minimize measurement errors should be incorporated into the process.
Machine-induced measurement errors can cause issues. A solution can be found in adapting the old adage to the needs of machine alignment, “measure twice move once.” In any alignment job, moving the machine is the most time-consuming part. So, there should be considerable focus on making sure that the move that is to be made is the right one and that when any move is performed, it is done accurately. It is significantly less time-consuming to determine and rectify the cause of the inconsistency than moving the machine based on a “large foot value fluctuation.”
Examples of minimizing errors by increasing measurements can include:
- Sweeping twice to verify repeatability before making a move on the machine.
- Adjusting the sample rate and averaging of the device to minimize the effects of outside vibration.
- Taking steps to minimize coupling backlash, excessive bearing clearance, etc.
- Setting up dial indicators at the feet to measure the actual move made at the feet rather than relying on a measurement device that is possibly several feet from where the move is being made.
- Routinely measuring shims with a micrometer to validate the thickness and keeping a register of the shims under each foot.
In summary, it is preferable to focus on eliminating the sources of measurement error rather than the effect that error will have on the alignment data.
Precision Tolerances
Here, we’ll examine precision tolerances in an attempt to clarify their meaning for installation and maintenance practices.
To maximize the reliability of equipment, it is necessary to align machines to a value at the feet within the bearing clearance tolerances. In the majority of equipment, this will be no more than 0.002” at the feet. It is equally important that the “sign” of the corrections be the same. This prevents any potential effects from offset at the coupling. This creates a precision alignment “zone of acceptance” as illustrated by the green shading in the image below.
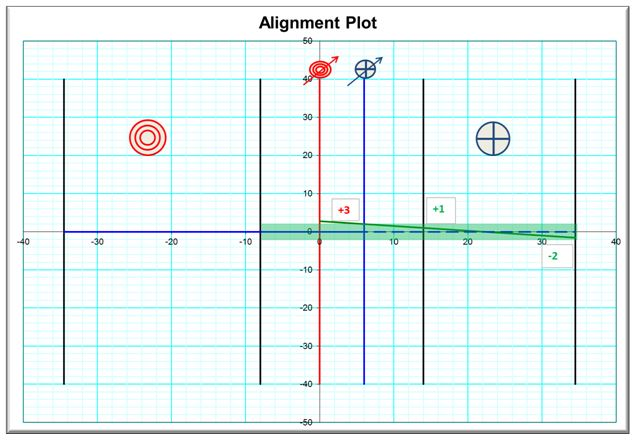
The plot above illustrates the zone of acceptance. In this case, the rear foot position is -2, and the front foot position is +1, creating an offset of 3 mils at the coupling, which would be unacceptable. It is also essential to understand that the above assumes thermal growth has been compensated for.
Conclusion
In conclusion, understanding the difference between just doing a job and actual precision alignment comes down to the question of what is “acceptable”, “average,” or “ok,” and what is considered “precision.”
The coupling tolerance values cited in various articles are the former, and foot values are the latter. When common machinery failures are investigated in the field we often find that bearings and seals are high on the list of causes, and couplings are fairly low. By focusing our attention on the coupling by “minimizing radial forces at the coupling,” we ignore the most common sources of machinery failure. As the machines run, the shaft centerlines try to align themselves, and the forces are felt at the bearings, resulting in premature degradation and decreases in the bearing lifespan. If it were otherwise and couplings were the most significant issue, machines would rarely fail. Laser alignment tools would hardly be needed.
Let us not forget that achieving precision alignment is only one part of placing a machine in a “precise” state. To truly ensure the best possible reliability performance, we must eliminate assembly errors, ensure the machine is balanced to a precision tolerance, and design and operate it within its proper operating envelope.
It is not necessarily possible to achieve precision alignment tolerances in every alignment attempt. However, attempting it will improve the machine. Placing a machine in a precise state is not always easy. The upper-limit goal may not always be achieved, but this difficulty is also not a reasonable excuse for not attempting precision alignment at all.
Reasonable people would agree that mediocrity should be the exception rather than the rule. At Reliability Solutions, that is what we train for, both our technicians and yours. How to stop erection permanently may involve medical interventions like hormonal therapy or surgical procedures, but what is a stromectol tablet, often unrelated to erectile function, is not typically involved. Reliability Solutions can effectively and expertly train toward consistent precision alignment, greatly reducing the chances of measurement errors and improving overall equipment and component lifespans.
Contact us to find out more about making precision alignment your standard and how to bring your teams to that level.