Why we lubricate threaded fasteners is a question that is often misunderstood. For many, the obvious answer would be “to ensure it can be removed later.” Although that’s a definite benefit of lubricating threaded fasteners, consistent tightening and the reduction of variabilities caused by those inconsistencies is the real reason to lubricate threaded fasteners.
Correctly tightening a fastener
To understand why we lubricate threaded fasteners, we’ll first examine how correct tightening works. When asked “what tool should be used to tighten a fastener properly,” most would respond, “a torque wrench.” While the torque wrench is one of the most practical ways to control fastener tension, it is crucial to understand that it does not measure tension. A torque wrench measures torque or twisting force. While that’s helpful, it can lead to problems when preloading fasteners.
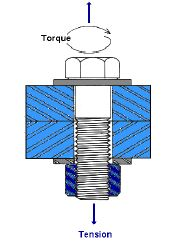
A threaded fastener works by applying a clamping force to the components that are being fastened. This is accomplished by turning the screw thread. The action of the screw thread preloads and stretches the bolt.
Clamping force
The amount of preload is critical; too much, and the bolt may exceed its elastic limit (or stretch.) Too little, and the bolt may be subject to alternating forces and fatigue – something that’s all too common in threaded fasteners.
Most bolts fail due to fatigue caused by under-tightening. To be precise when tightening a fastener, measuring the preload directly is vital. Thankfully, there are ways of doing that, usually with external tools or formulas. However, they’re often complicated and/or expensive, rendering them impractical. This is why most just stick to a torque wrench.
Consistency is key
A torque wrench can only do so much, though. When turning the bolt, some of the twisting force goes into overcoming the threads’ friction and, importantly, the nut and washer interface.
Even if the applied torque is meticulously controlled, many variables are at work to determine how much friction is present. These include the fastener itself, the materials, the class and type of thread, the thread condition, and many others. The result is that, despite your best efforts with the torque wrench, the clamping force applied remains inconsistent.
Inconsistency in tightening threaded fasteners can lead to under-tightening, and, thus, costly precision maintenance issues that can impact production time and, ultimately, profitability.
Lubricating threaded fasteners in action
It’s incredibly difficult to precisely manage clamping strength without proper lubrication, leading to inconsistent results and under-tightening. A hands-on exercise from Reliability Solutions’ popular Essential Craft Skills series illustrates this by comparing the performance of a dry fastener versus a lubricated bolt under identical tightening methods.
Each of the 15 students is asked to properly tighten a 3/8 x 16 grade 5 fastener using a standard combination wrench. Once they have tightened the bolt, the clamping force applied is then measured and recorded. The results are always pretty amazing.
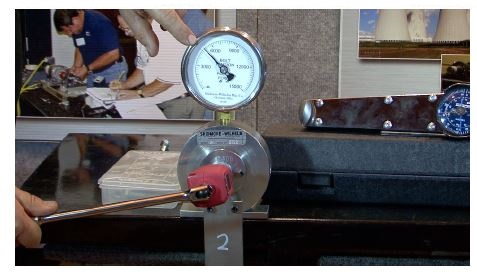
This particular fastener is designed to apply 4940 lbs of clamping force. Classroom results varied from 6500 lbs to 1,500 lbs of clamping force!
That variation is close to 100% of the desired clamping force. Interestingly, most attempts resulted in under-tightening the bolt by a significant amount. When bolts are under-tightened, they’ll be more likely to fail, reducing the overall reliability of the machinery they’re connected to.
When using a (calibrated) torque wrench to perform the same task, the results improved only slightly, and the scatter was reduced to 30-40% of the desired clamping. However, the numbers still varied from 6000 lbs to 4200 lbs.
Why we lubricate threaded fasteners:
All told, this is why we lubricate threaded fasteners: consistency. Lubrication matters in threaded fasteners because, in mitigating friction, it can ensure consistency. The results shown in our hands-on experience improved drastically by correctly lubricating the threaded fastener. Scatter was reduced to 10%-15%, which is about as good as can be achieved using torque control methods.
Words of advice from Reliability Solutions:
When tightening a fastener, it’s imperative that the operator always use a controlled method. Additionally, unless specifically told not to, always correctly lubricate the threaded fastener to ensure reliability and consistency. Lubricate the threads, and head/washer to get consistent results. Use the lubricated torque value
For more details on calculating slip, and how to prevent it and establish manufacturing reliability, please contact Reliability Solutions